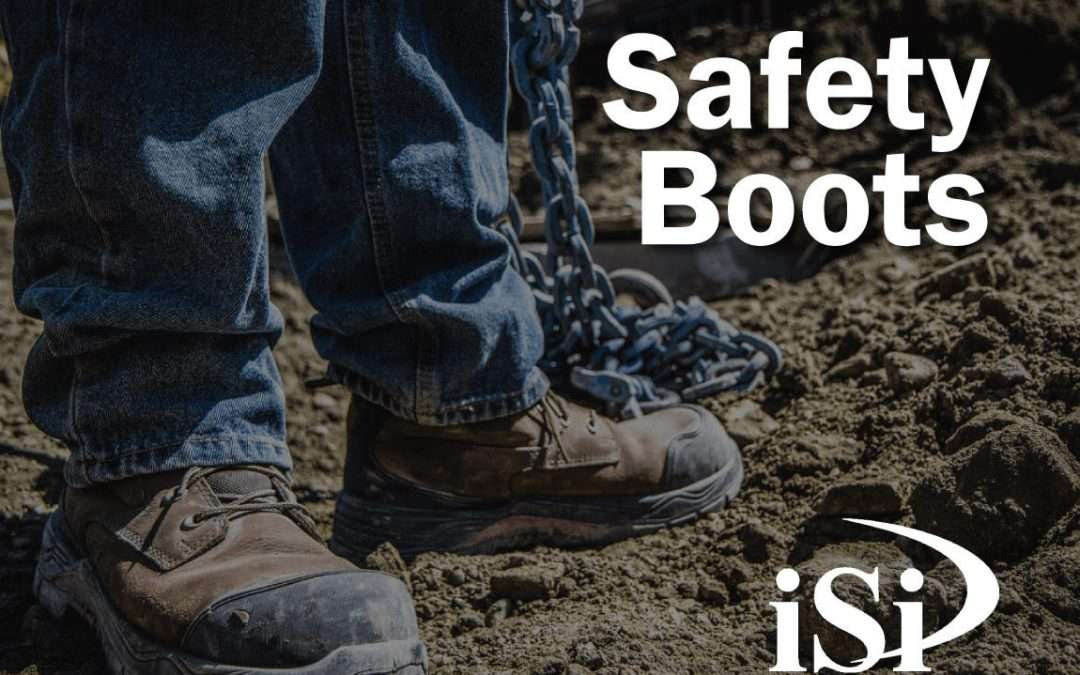
Safety Boots: What You Need To Know
Many types of jobs require the use of boots for safety purposes. Some jobs just need regular boots while others require steel or composite toes.
Toe Composition
Steel toe boots have a steel cap over the toe to prevent your feet from being crushed by objects falling on them or rolling over them. Composite toe boots can have toes made of Kevlar, carbon fiber, fiberglass or carbon nanocomposites (composite cylinders arranged in beehive pattern mixed with fiber resin). Composite toes don’t conduct heat, cold, nor electricity, and are thicker but lighter weight than a steel toed boot. They are not as impact-resistant. There are also alloy toe boots such as aluminum or titanium. These are a little less protective but lighter weight than steel toe boots. They can be a little more expensive as well.
Best Practices
- Always buy boots that meet ASTM standards for impact and compression and always buy the types of boots your company recommends or requires. Your company has conducted formal PPE assessments to determine the safest types of boots for the work you do.
- Always wear the proper socks. Moisture wicking socks are better than cotton socks because cotton socks will tend to create moisture leading to uncomfortableness, foot pain and faster damage to the inside of your boots.
- Keep the insides of your boots dry and maintain the waterproofing on the outsides of them.
- Remove mud, dirt, clay, and gunk—they’ll dry out the leather.
- You can increase the life span of your boots by using premade orthotic insoles.
Checking the Wear
Worn out boots not only are uncomfortable, but they are unsafe. Not replacing them when they’re worn out can cause foot/back/leg pain, foot stress and ingrown toenails and can increase your chances of falling, especially in slippery environments. Check for wear by looking at:
- Soles, outsides of the heels, and balls of the shoe for wear. Are soles separating? Sole separation can cause instability, reduce shock absorption and let moisture or chemicals in.
- Tears, holes, cracks and external damage—Damage like this can make them less electrical and chemical resistant and more susceptible to foot punctures
- Internal damage-Look at the inside, the tongue and look for the stitching. Torn insulation can let in moisture and chemicals. The instep shouldn’t be bunching up.
Finding and Trying on Boots
- Wear the socks you’ll be wearing with the boots when you try them on
- Your heel shouldn’t come up out of the boot or rub on the back. It shouldn’t move more than a quarter of an inch. As leather conforms to your foot, it will mold to your heel and slight slippage will reduce.
- You should have an inch of room in your toes but your toes shouldn’t slide forward when you walk.
- The boot should be secure on the sides and top of your foot but not be painful.
- Make sure the inner stitching nor the tongue rub on your foot.
- When trying them on put them through their paces because you want to make sure they’re right for you: walk, run, hop, do knee raises, stand in place, flex your foot, and carefully roll your ankles and stand on the sides of your foot to test ankle support. If you have red spots on your feet after trying them on, those are the places where the shoe will rub.
- Always try on boots on both of your feet. Your feet change sizes throughout the day, so try boots on in the afternoon when your feet tend to be bigger.
- If your feet are two different sizes, purchase the boot to fit your larger foot and wear a heel insert for your smaller foot.
- If you have flat feet, taller boots with stronger insoles may fit better.
- Boot companies traditionally have you order 1/2 size smaller than your sneaker size. For steel toe boots, you may need to order the same size as your sneaker size, or even a 1/2 size larger than your normal shoe size. If you wear thick socks, the larger boot sizes will be needed to accommodate those.
Free Safety Toolboxes Delivered to Your Inbox
We email out a different safety toolbox like this one every other week for you to share with your teams. Sign up today by emailing Tami at [email protected].
Need Help?
Need assistance with your OSHA compliance tasks? How can we make compliance easier for you?