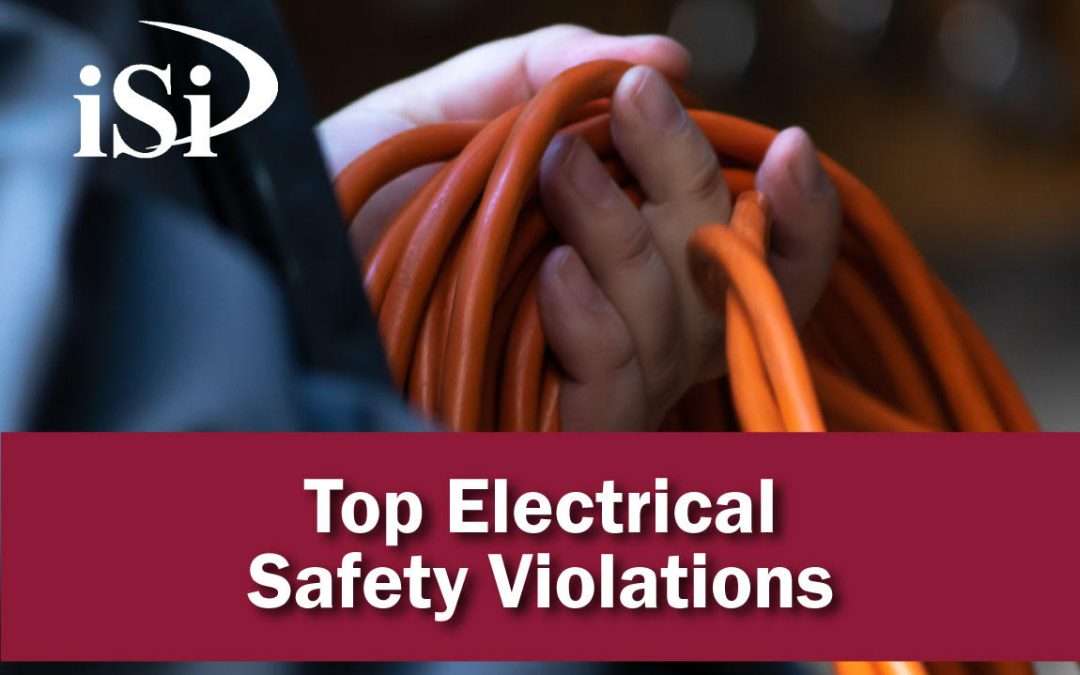
Top Electrical Safety Violations
In honor of May’s electrical safety month designation, here’s a list of OSHA’s most common electrical safety violations found in General Industry and Construction:
Listed or Labeled Equipment 1910.303(b)(2) & 1926.403(b)(2)
This is OSHA’s most cited electrical standard. It reads “Listed or labeled equipment shall be installed and used in accordance with any instruction included in the listing or labeling.” So this is both using equipment approved by a National Recognized Testing Laboratory (NRTL) such as UL (Underwriters Laboratories), FM (FM Approvals), and ETL (Intertek). It’s also for using equipment in ways it wasn’t intended such as daisy chaining extension cords or using relocatable power taps (power strips) improperly.
Flexible Cords 1910.305(g) & 1926.405(g)
Flexible cords in this standard is extension cords. You cannot use extension cords as a substitute for fixed wiring. They must have sufficient strain relief and you cannot attach them to building surfaces. Also, never run extension cords through floors, ceilings, or door and window openings.
Clearance Around Electrical Equipment < 600 V is 1910.303(g)(1) & 1926.403(i)(1), > 600 V is 1910.303(h)(3) & 1926.403(j)(3)
Leave sufficient access and working space around electrical equipment. The depth and width of the working space, number of entrances and minimum headroom required depends on voltage. For 600V or less an area 3 feet deep in front of the panel face and equal to the width of the panel or 30 inches wide (whichever is greater) must remain clear around all electrical panels to allow for access to the panel. Do not block access to electrical equipment for emergency access.
Guarding/Enclosing Electrical Equipment < 600 V is 1910.303(g)(2) & 1926.403(i)(2), > 600 V is 1910.303(h)(5) & 1926.403(j)(3)
Live parts of electrical equipment at 50 volts or higher must be guarded against accidental contact by using a cabinet or other enclosure, by putting it in a room or vault that’s only accessible to qualified persons only, by placing it on an elevated balcony, gallery or platform so unqualified persons cannot access it, or by putting it 8 ft. or higher above the working surface. If equipment is likely to be exposed to physical damage, then sufficient strength guarding is required. High voltage equipment (> 600 V) must be physically restricted (e.g. locked) and have warning sign stating “high voltage.” Rooms with guarded live parts must also be labeled with warning signs forbidding unqualified persons to enter.
Unused Openings in Junction Boxes 1910.305(b)(2)(i) and 1910.305(b)(ii)
This standard is focused on electrical outlet covers, circuit breaker panel doors, covers and boxes, and junction box knockout covers. Close or cover any unused openings to protect against exposure to energized parts.
Grounding Path 1910.304(g)(5) and 1926.404(f)(6)
The path to ground from circuits, equipment, and enclosures shall be permanent, continuous, and effective. Build-up of voltages can lead to electrical shock, fire, arc flash, and downtime. The grounding system serves as a backup pathway that provide an alternative route for electrical current to follow back to ground in case of wiring system problems. Common mistakes include: failing to measure grounding system after install, not reattaching ground paths after relocating, replacing, or removing equipment for repairs, using ground wire incorrectly – i.e. not using gradual bends, short wire lengths and secure connections, and choosing incorrect ground wire.
Inspecting Cord and Plug Equipment 1910.334(a)(2)(i), 1910.304(b)(3)(ii)(c)(3) & 1926.404(b)(1)(iii)(c)
Portable cord and plug connected equipment and flex cord sets need to be visually inspected before each use on any shift for external defects and evidence of possible internal damage. Once it’s put in place if it’s not exposed to damage it will not need to be visually inspected until it’s relocated.
Some visual checks include:
- Visible damage to equipment, wall disconnects, enclosures and devices
- Defects and missing, bent, or broken plug prongs
- External sheaths of power supply cords for cuts, frays, twists, or damage
- Ensure inner cores of power supply cords are not exposed where they connect to equipment, plus and/or sockets
- Ensure inner core of power cord is not exposed / twisted along cord length
- Ensure electrical devices have proper ground with 3-prong plug
- Keep power cords and hoses clear of walkways / equipment paths, and away from heat, oil, sharp edges and moving parts that can damage sheath or insulation
- Use only approved extension cords with proper gauge wire for length of cord and voltage requirements of equipment to prevent overheating
- Pull the plug, not the cord when unplugging equipment
Working With Energized Electrical Equipment
Energized electrical parts (>50 V) must be de-energized before work, unless de-energizing introduces additional or increased hazards, or if it’s infeasible due to equipment design or operational limitations. It requires lockout / tagout and only trained and qualified persons may perform energized work. Safe work practices include:
- Job briefings
- Energized electrical work permits
- Personal protective equipment
- Insulated tools
- Written safety program
- Alerting techniques (e.g. barricades, signage, attendants)
Training Qualified Persons
Qualified persons are capable of working safety on energized circuits and familiar with and utilize proper precautionary techniques, PPE, insulating and shielding materials, and insulated tools. Training for qualified persons at a minimum should teach the ability to distinguish exposed energized parts from other parts, how to determine nominal voltage of exposed energized parts, and the ability to determine clearance distances and voltages. NFPA 70E recommends refreshers for qualified personnel every 3 years. Training is also required for unqualified persons if exposed to shock hazards. For persons operating electrical equipment under normal conditions at 50-600V, training that covers safe work practices such as wearing leather gloves, flame resistant clothing, body positioning when throwing disconnects, etc. would be a good idea. Remember, electrical employees are only qualified to the level of their training. You need appropriate training and experience before you’re allowed to do any electrical work.
PPE
PPE is required for the head to protect from electric shock or burns due to contact, eyes and face to protect from arc flashes or flying objects, the body to protect from the temperatures of arc flashes, the hands to protect from shock and arc flash, and the feet to protect from arc flash. Training should include when and what PPE is necessary, how to don, doff, adjust and wear it, PPE’s limitations, and proper care, maintenance, useful life and disposal.
For more questions about electrical safety compliance, or to schedule training for your workers, contact iSi today!
Need Help?
Do you have any electrical safety issues? What else is going on at your facility? iSi can help find other areas you may also need to look at and can give you a checklist to help you determine which areas need to be tackled first.
Questions?
Does this apply to your company? Do you have questions? Contact us!
Receive News to Your Inbox
We send our articles by email whenever we add a new one. Don’t miss out! Sign up for our blog today.
Request a Quote
iSi can provide assistance in this area. How can we help? Ask us for a price quote.