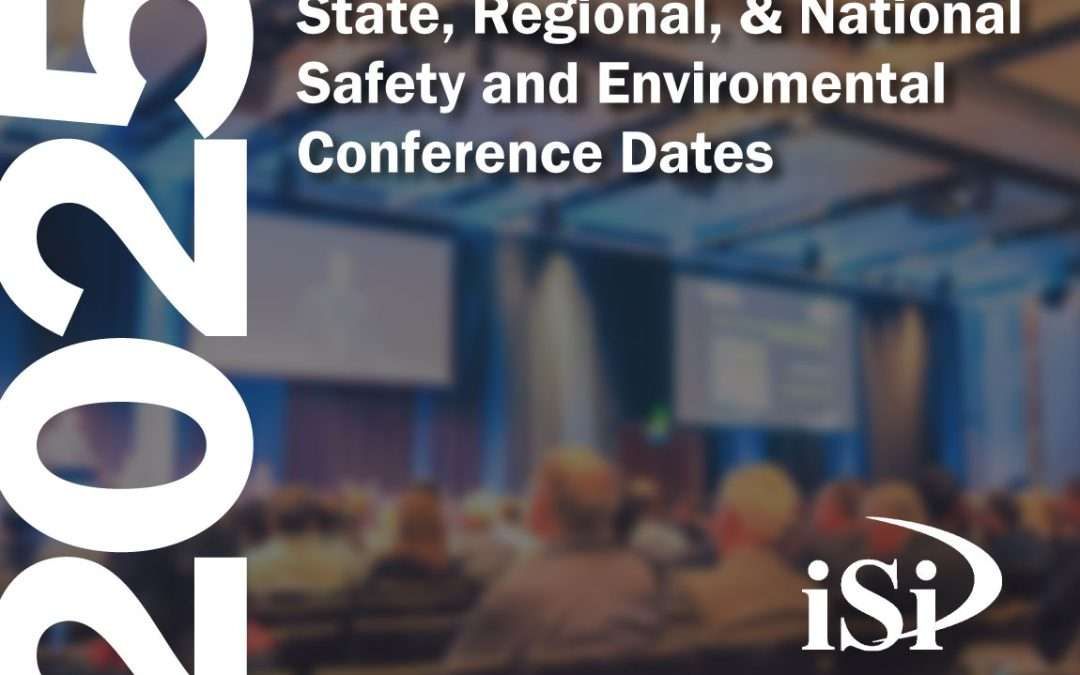
State, Regional and National Safety and Environmental Conferences for 2025
We exhibit and speak at many different safety and environmental conferences throughout the region. What’s the schedule look like for 2025?
Here is a list of some upcoming state, regional and national safety and environmental conferences that you may want to add to your calendar. (For now, we’re listing the ones near where we have offices. )
We will work to keep this list updated as we find out changes, if any.
Central U.S. / Region VII
Region VII (KS, MO, IA, NE)
Midwest Environmental Compliance Conference (MECC)
Sept. 15-16 | Overland Park | Learn More
Region VII VPPPA Midwest Safety and Health Conference
TBD | Des Moines | Learn More
Kansas
KDHE Environmental Conference
Aug. 13-14 | Manhattan, KS | Learn More
Kansas Safety and Health Conference
Oct. 13-17 | Manhattan, KS | Learn More
Missouri
Mid-America Safety, Health & Environmental Conference and Expo
TBD | Springfield | Learn More
Greater St. Louis Safety & Health Conference
TBD | St. Louis | Learn More
Missouri Hazardous Waste Seminar
TBD | Learn More
Safety & Health Council of Western Missouri & Kansas SAFECONEXPO
May 14-16 | Lake Ozarks, MO | Learn More
Nebraska
Nebraska Safety & Health Summit
Nov. 4 | Omaha | Learn More
Iowa
Hawkeye on Safety
TBD | Coralville | Learn More
Iowa Governor’s Safety & Health Conference
Oct. 8-29 | Altoona | Learn More
Central U.S. / Region VI
Region VI (OK, TX, NM, LA, AR)
Region VI VPPPA
May 19-22 | Corpus Christi, TX | Learn More
Oklahoma
Oklahoma Safety and Health Conference
June 3-5 | Tulsa | Learn More
Environmental Federation of Oklahoma (EFO) Annual Meeting & Trade Show
Oct. 13-15 | Tulsa | Learn More
Southeast / Region IV
Region IV (GA, AL, MS, KY, TN, NC, SC, FL)
Region IV VPPA Safety + Symposium
Aug. 11-14 | St. Louis, MO | Learn More
Georgia
Georgia Environmental Conference
Aug. 20-22 | Jekyll Island | Learn More
Georgia Safety, Health and Environmental Conference
Sept. 3-5 | Savannah | Learn More
Tennessee
Chattanooga Regional Manufacturers’ Association Environmental, Health and Safety Summit
TBD | Chattanooga | Learn More
Tennessee Environmental Network Show of the South
May 14-16 | Chattanooga | Learn More
Alabama
Alabama Governor’s Safety and Health Conference
Aug. 25-27 | Orange Beach | Learn More
Manufacture Alabama HR, Safety & Environmental Conference
July 30-31 | Birmingham | Learn More
North Carolina
NC Statewide Safety Conference
TBD | Learn More
Carolina Star Safety Conference
Sept. 17-19 | Greensboro | Learn More
Eastern Carolina Safety & Health Conference
Apr. 10-11 | Atlantic Beach | Learn More
South Carolina
South Carolina Environmental Conference
Mar. 9-12 | Myrtle Beach | Learn More
ASSP Region VI Conference
Sept. 17-19 | Myrtle Beach | Learn More
NSC Southeast Regional Conference & Expo
Sept. 12-18 | Denver | Learn More
National Conferences
American Society of Safety Professionals (ASSP) Conference and Expo
July 22-24 | Orlando, FL | Learn More
National Safety Council (NSC) Safety Congress
Sept. 15-17 | Denver, CO | Learn More
Associated General Contractors (AGC) Construction Safety, Health & Environmental Conference
TBD | St. Louis, MO | Learn More
Associated General Contractors (AGC) Construction Safety & Health Conference
July 22-24 | Minneapolis, MN | Learn More
Alliance of Hazardous Materials Professionals (AHMP) National Conference
Sept. 8-11 | Louisville, KY | Learn More
National Association of Environmental Professionals (NAEP) Annual Conference and Training Symposium
Apr. 28 – May 1 | Charleston, SC | Learn More
National Environmental Health Association (NEHA) Annual Education Conference & Exhibition
July 14-17 | Phoenix, AZ | Learn More
Which safety and environmental conferences did we miss? Let us know by emailing us here.
Stay Informed of EPA & OSHA Updates!
We send out our blog articles via email. Don’t miss an article!