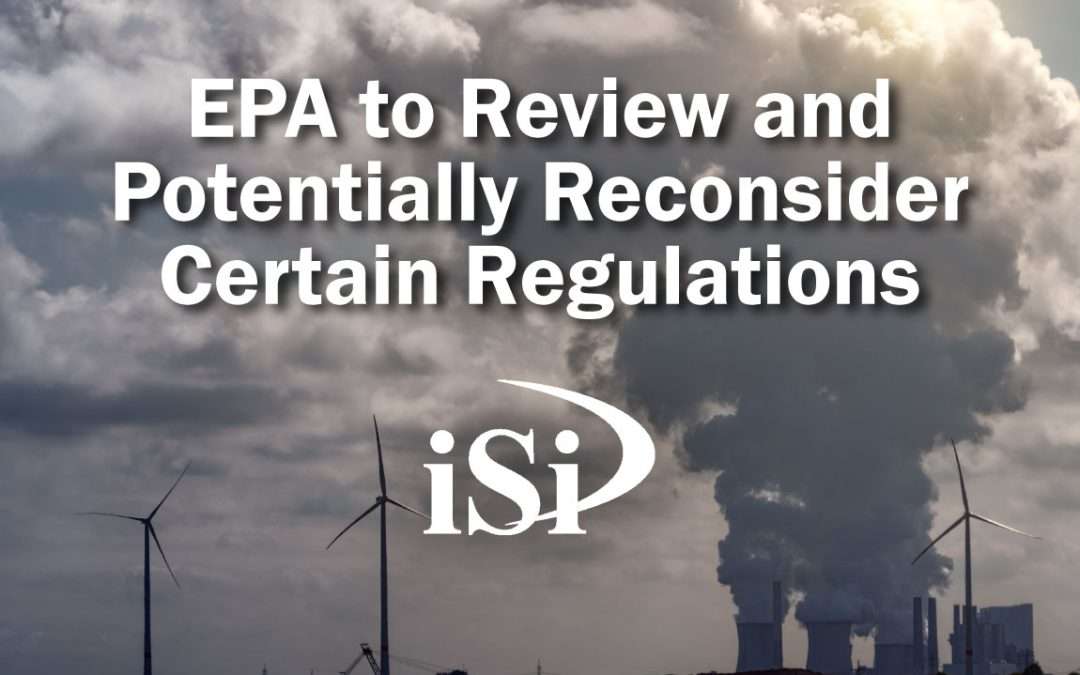
EPA to Review and Potentially Reconsider Recently Created Regulations
Other Agencies May Follow Suit
EPA’s new Administrator Lee Zeldin says the agency is going to focus on a new initiative to help return EPA to its core mission of conservation rather than “environmentalist radicalism” and regulation. Called “Powering the Great American Comeback,” it will focus on 5 goals:
- Clean air, land, and water for every American;
- Restoring American energy dominance;
- Permitting reform, cooperative federalism, and cross-agency partnership;
- Making the U.S. the AI Capital of the World; and,
- Protecting and bringing back American auto jobs.
A big part of this effort is to review regulations created in past administrations that targeted the energy sector, oil and gas and the auto industry or were altered for climate change considerations or other presidential directives. The following regulations are already on the list for review:
Goal: Unleash American Energy
Regulations to be Reconsidered:
- Mandatory Greenhouse Gas (GHG) Reporting
- The new Risk Management Plan Program Rule changes from May 2024 for oil and natural gas refineries and chemical facilities
- Clean Power Plan 2.0 for power plants
- Oil and gas industry regulations OOOO b/c (Quad O)
- Mercury and Toxics Standards (MATS) for coal-fired power plants
- Limitations, guidelines and standards (ELG) for Steam Electric Power Generating Industry to ensure low-cost electricity while protecting water resources
- Wastewater regulations for oil and gas development
Goal: Lowering the Cost of Living for American Families
Regulations to be Reconsidered:
- Multiple National Emissions Standards for Hazardous Air Pollutants (NESHAPs) for energy and manufacturing
- Redirecting enforcement resources to relieve the economy of unnecessary bureaucratic burdens, using enforcement discretion
- Particulate Matter National Ambient Air Quality Standards (PM 2.5 NAAQS)
- Car GHG Rules for light-duty, medium-duty and heavy-duty vehicles that provided foundation for electrical vehicle mandate
- Technology Transition Rule – rule that forced the use of certain technologies that raised costs on food for grocery stores and semiconductor manufacturing
- Regional Haze Program
- Social Cost of Carbon program
- Environmental Justice and DEI arms of EPA
- 2009 Endangerment Finding and regulations
Goal: Advancing Cooperative Federalism
Regulations to be Reconsidered:
- Ending the Good Neighbor Plan that was used to expand federal rules to more states and sectors beyond the traditional focus and led to the rejection of nearly all State Implementation plans
- Clearing up massive backlog with State Implementation Plans and Tribal Implementation Plans the previous administration refused to resolve
- Exceptional Events – Rulemaking to work with states to prioritize allowance of prescribed fires withing state and tribal implementation plans
- Reconstituting the Science Advisory Board and Clearn Air Scientific Advisory Committee
- Prioritizing coal ash program to expedite state permit reviews and update coal ash regulations
- Utilizing enforcement discretion to further North Carolina’s recovery from the hurricane
Other Agency Policies and More Reviews Possible
There were a number of regulations and policies that were changed in the previous administration due to Executive Orders which required agencies to consider climate change and environmental justice in rulemaking and policy creation. Agencies like EPA, OSHA and DOT made similar priority lists and highlighted how they were complying with this order. For example, EPA made a change to the Facility Response Plan regulation in the Clean Water Act in March 2024 that required worst case planning to now include planning for disasters caused by weather events brought on by climate change. They also created maps of areas that could be impacted by environmental justice issues and the agency and states were to develop plans to address those.
With the change in administration, it’s unlikely that the above items will be the only regulations to be reviewed at EPA. They are likely to be the first among many and you may eventually see similar efforts with other agencies as well.
For example, DOT recently rescinded two memorandums which required the agency to consider social justice and climate change considerations in infrastructure projects. DOT says they created additional time delays and financial burdens. Agencies like the Associated General Contractors, the American Highway Users Alliance, and the American Road and Transportation Builders Associations applauded the DOT, saying the memo directives also created uncertainty for state departments of transportation and construction companies.
We will keep an eye out for other efforts to reduce/change regulations within EPA, OSHA and DOT and keep you updated.
Need Help?
Which EPA environmental deadlines apply to you? Let iSi help!