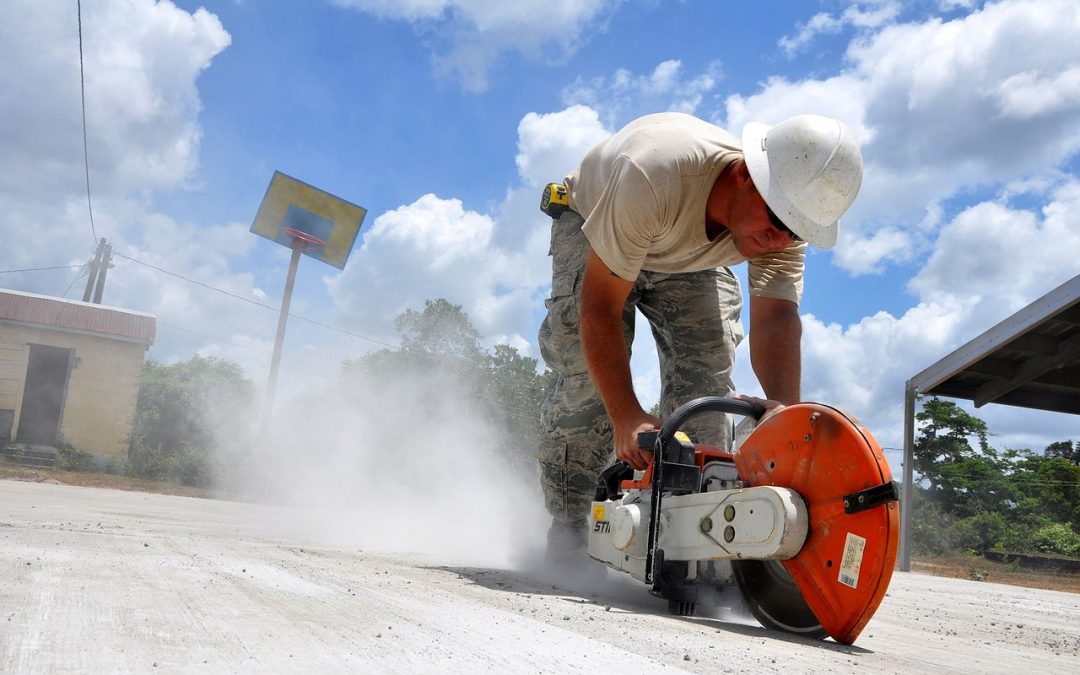
OSHA’s Silica Rule for Construction
Webinar
Watch our webinar to determine how these regulations apply to your company.
Construction requirements are more geared toward methods of controlling exposures and silica exposure sampling.
Table 1
The construction standard has a table of common construction tasks and the instructions on how to control dust for each. This is referred to as Table 1. As long as your company is following the actions required of Table 1, your company will not be required to conduct sampling and won’t be subject to the PEL requirement. Please note that some of the instructions in Table 1 require workers to wear respirators. If your workers currently do not wear respirators, use of respirators will trigger the need to comply with 29 CFR 1910.134 for use of respirators. This would include developing a written respiratory protection program, annual respirator physicals, annual respirator training and annual respirator fit-testing. Contact us here for a copy of Table 1
What if You Don’t Want to Follow Table 1? More on Silica Exposure Sampling
Employers who choose not to follow the guidance of Table 1 will then be subject to the requirements of the action level and the PEL. This triggers the additional sampling and monitoring requirements that the general industry standard requires. Employers will need to conduct exposure monitoring for silica if the potential for exposure could be at or above an action level of 25 µm3 (micrograms per cubic meter of air), averaged over an 8-hour day. The PEL is 50 µm3, averaged over an 8-hour day (the old PEL for construction was 250 µm3).
Affected employees must be notified in writing of assessment results and if it’s above the PEL, the notification will need to include what’s being done to control exposures. If results are above the action level but below the PEL, sampling will need to occur every 6 months until exposures are below the action level for 2 consecutive measurements. If results are above the PEL, sampling will need to occur every 3 months until exposures are below the action level for 2 consecutive measurements. Unless the potential for silica exposure is 0%, if there’s even a slight potential for silica exposures, it’s best to conduct the sampling to know exactly what your exposure levels are for documentation purposes.
Documentation of your exposure assessment is very important for your recordkeeping files and shows due diligence with the standard. Anyone above the PEL and not using Table 1 must take measures to protect workers from exposure. Dust controls need to be used to protect workers from exposures above the PEL. When dust controls don’t work, respirators are required.
Other Requirements for Construction
- Medical Exams — Medical exams that include chest X-rays and lung function tests must be offered to workers who are required by the standard to wear respirators for 30 or more days per year. These exams must be offered every 3 years.
- Competent Person — Your company will need to designate a competent person to implement the your written exposure control plan.
- Restricted Access — Procedures for how your company will restrict access to work areas where high exposures may occur must be included in your written exposure control plan.
Compliance Deadlines
Employers must comply with all requirements of the standard by September 23, 2017. If your company chooses to use exposure sampling and laboratory analysis, then the compliance deadline for laboratory evaluation of exposure samples is June 23, 2018.
Now What? How Can iSi Help You With This Standard?
iSi is here to help your company comply with this new standard. We can assist with:
- Compliance Determinations, Audits and Checklists – Helping you determine if this standard applies to you, evaluating your site for exposure potential, determining areas needing warning signs or restricted access, and making a compliance checklist for you
- Exposure Sampling – Sampling your facility or construction sites for exposure levels, arranging for lab analysis of samples, preparing documentation for recordkeeping, and preparing your written employee notices
- Written Program Development – Preparing your exposure control plan or respiratory protection program
- Training – Silica training and respiratory protection training
- Respirator Fit-Testing – Annual respirator fit-testing (after your medical surveillance is complete)
- Answering Questions – Our safety and industrial hygiene experts on-staff can help you with any other questions you may have.
Contact us today with questions or pricing requests.
Webinar
Attend our webinar to determine how these regulations apply to your organization.
Construction requirements are more geared toward methods of controlling exposures and silica exposure sampling.
Table 1
The construction standard has a table of common construction tasks and the instructions on how to control dust for each. This is referred to as Table 1. As long as your company is following the actions required of Table 1, your company will not be required to conduct sampling and won’t be subject to the PEL requirement. Please note that some of the instructions in Table 1 require workers to wear respirators. If your workers currently do not wear respirators, use of respirators will trigger the need to comply with 29 CFR 1910.134 for use of respirators. This would include developing a written respiratory protection program, annual respirator physicals, annual respirator training and annual respirator fit-testing. Contact us here for a copy of Table 1
What if You Don’t Want to Follow Table 1? More on Silica Exposure Sampling
Employers who choose not to follow the guidance of Table 1 will then be subject to the requirements of the action level and the PEL. This triggers the additional sampling and monitoring requirements that the general industry standard requires. Employers will need to conduct exposure monitoring for silica if the potential for exposure could be at or above an action level of 25 µm3 (micrograms per cubic meter of air), averaged over an 8-hour day. The PEL is 50 µm3, averaged over an 8-hour day (the old PEL for construction was 250 µm3).
Affected employees must be notified in writing of assessment results and if it’s above the PEL, the notification will need to include what’s being done to control exposures. If results are above the action level but below the PEL, sampling will need to occur every 6 months until exposures are below the action level for 2 consecutive measurements. If results are above the PEL, sampling will need to occur every 3 months until exposures are below the action level for 2 consecutive measurements. Unless the potential for silica exposure is 0%, if there’s even a slight potential for silica exposures, it’s best to conduct the sampling to know exactly what your exposure levels are for documentation purposes.
Documentation of your exposure assessment is very important for your recordkeeping files and shows due diligence with the standard. Anyone above the PEL and not using Table 1 must take measures to protect workers from exposure. Dust controls need to be used to protect workers from exposures above the PEL. When dust controls don’t work, respirators are required.
Other Requirements for Construction
- Medical Exams — Medical exams that include chest X-rays and lung function tests must be offered to workers who are required by the standard to wear respirators for 30 or more days per year. These exams must be offered every 3 years.
- Competent Person — Your company will need to designate a competent person to implement the your written exposure control plan.
- Restricted Access — Procedures for how your company will restrict access to work areas where high exposures may occur must be included in your written exposure control plan.
Compliance Deadlines
Employers must comply with all requirements of the standard by September 23, 2017. If your company chooses to use exposure sampling and laboratory analysis, then the compliance deadline for laboratory evaluation of exposure samples is June 23, 2018.
Now What? How Can iSi Help You With This Standard?
iSi is here to help your company comply with this new standard. We can assist with:
- Compliance Determinations, Audits and Checklists – Helping you determine if this standard applies to you, evaluating your site for exposure potential, determining areas needing warning signs or restricted access, and making a compliance checklist for you
- Exposure Sampling – Sampling your facility or construction sites for exposure levels, arranging for lab analysis of samples, preparing documentation for recordkeeping, and preparing your written employee notices
- Written Program Development – Preparing your exposure control plan or respiratory protection program
- Training – Silica training and respiratory protection training
- Respirator Fit-Testing – Annual respirator fit-testing (after your medical surveillance is complete)
- Answering Questions – Our safety and industrial hygiene experts on-staff can help you with any other questions you may have.
Contact us today with questions or pricing requests.