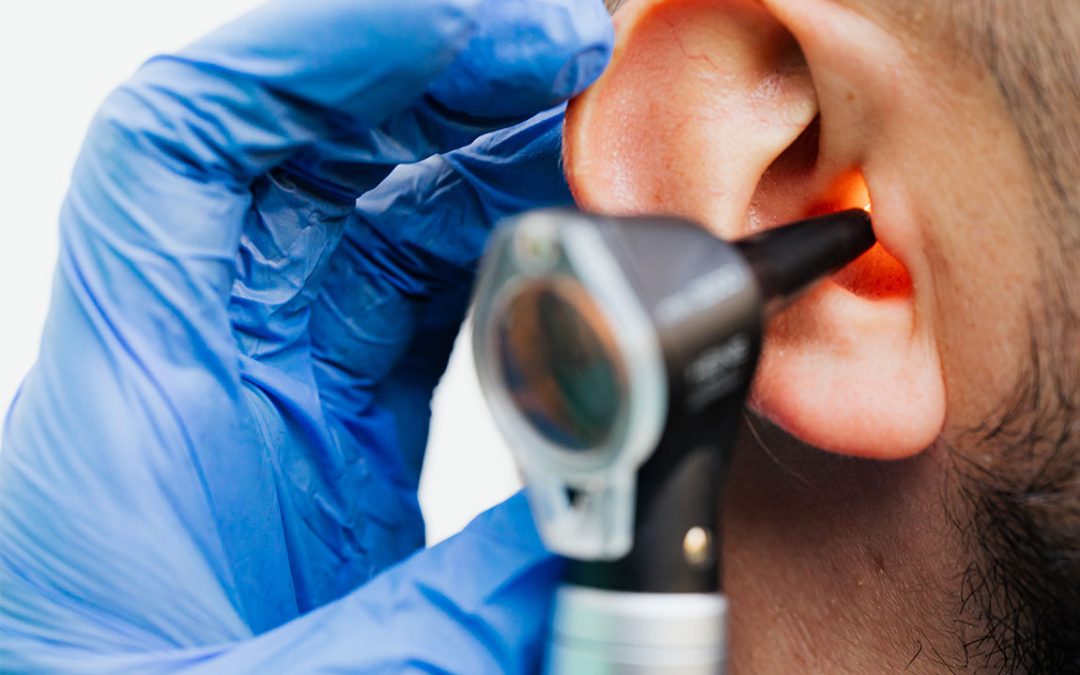
Ototoxicity – When Chemicals (yes, chemicals) Cause Hearing Loss
Need Help?
Let iSi help you determine what to do about ototoxic chemicals and noise exposures at your facility!
The effects of chemical exposures in the workplace has been highly documented. Chemicals can affect you when you breathe them in, ingest them, inject them or absorb them through your skin. However, did you know that chemicals can cause hearing loss too?
What is Ototoxicity?
Chemicals which can contribute to hearing loss are called “ototoxicants” and the hearing loss itself is considered to be “ototoxicity.” Ototoxic chemicals reach the inner ear, connected pathways and nerve fibers through the blood stream or through the ear’s hair cells. Hearing losses can range from sound distortion to the inability to detect two sounds with similar frequencies to inabilities to detect time gaps between sounds or localize sound.
The problem increases when there is a noise exposure combined with the exposure to an ototoxicant. Ototoxic chemicals make a bigger impact on noise exposure, especially impulse noise. Ototoxic chemicals plus noise becomes worse than just the noise alone or the chemical alone. The noise levels do not even need to be above OSHA’s Permissible Exposure Limit (PEL) standards. It’s the combination of the two which causes the greatest damage.
Which Chemicals Are Considered Ototoxic?
- Pharmaceuticals: aspirin, some antibiotics, NSAIDs, loop diuretics
- Tobacco smoke
- Solvents, degreasers and paints containing toluene, p-xylene, styrene, ethylbenzene, methylstyrene, trichlorethylene, carbon disulfide, n-propylbenzene or n-hexane
- Carbon monoxide
- Hydrogen cyanide
- Nitriles: 3-butenenitrile, cis-2-pentenenitrile, acrylonitrile, cis-crotononitrile and 3,3’-iminodipropionitrile
- Metals and compounds: mercury, lead, organic tin and germanium dioxide
- Pesticides: pyrethroids, hexachlorobenzene, insecticides or organophosphates
- Some limited research has also speculated arsenic, cadmium, halogenated hydrocarbons, bromates, alkylic compounds and manganese may also affect ototoxicity
Which Industries or Operations May be Affected?
- Manufacturing
- Construction
- Printing
- Painting
- Fueling vehicles and aircrafts
- Firefighting
- Weapons firing (Military)
- Pesticide spraying
How Do You Test for Otoxicity?
Determining whether you have the potential for this condition is primary. First, conduct a risk assessment to determine if your operations could be affected.
Check the Toxological Information section of the chemical’s Safety Data Sheet (SDS Section 11) to see if the chemical is considered a neurotoxicant. If there is nothing listed in this section, often other clues can be found in the SDS such as general toxicity, nephrotoxicity or if the chemical produces reactive free radicals.
From there, exposure limits and thresholds are dependent on different factors such as the chemical itself, exposure routes, concentration, duration, noise exposure and individual risk factors such as age. Workplace sampling will be able to help you quantify your exposures.
Audiogram tests can show early onset of hearing impairments and threshold shifts. However, they cannot tell you the difference between whether the impairment is noise-related or ototoxic-related. If you have complaints of hearing loss, investigate whether ototoxicity could be a factor.
The American Conference of Governmental Industrial Hygienists (ACGIH) recommends periodic audiograms for those who have noise exposures combined with carbon monoxide, hydrogen cyanide lead and solvent mixtures. When there’s not a noise exposure, ACGIH still recommends audiograms be used when workers have the potential to be exposed to ethylbenzene, styrene, toluene or xylene.
PPE and Training Requirements
Make sure you reduce the effects of ototoxic chemicals in your workplace either through controls such as isolation, limiting exposures, or eliminating unnecessary tasks, or through the use of PPE. Conduct your PPE assessment per OSHA rules. You may need to include proper hearing protection, as well as PPE which can prevent inhalation (respirators), or absorption through the skin (chemical gloves, arm sleeves, aprons).
If you have a potential for ototoxic chemical exposure, this also needs to be included in your Hazard Communication (HAZCOM) training.
Does This Affect You?
Do you have the potential for ototoxicity in your workplace? iSi can help you make that determination, conduct your risk assessment, and/or quantify your exposures through sampling. Contact us today!


Contributing:
Ryan Livengood
International Hazardous Materials Logistics Manager | EHS Regulatory Trainer
As a former corporate environmental, health and safety manager, Ryan has a vast experience in working with both environmental and safety compliance issues in multiple states. His specialties include national and international dangerous goods transportation, hazardous waste, environmental compliance, industrial hygiene and safety compliance. He is also an ISO 14001 Lead Auditor.