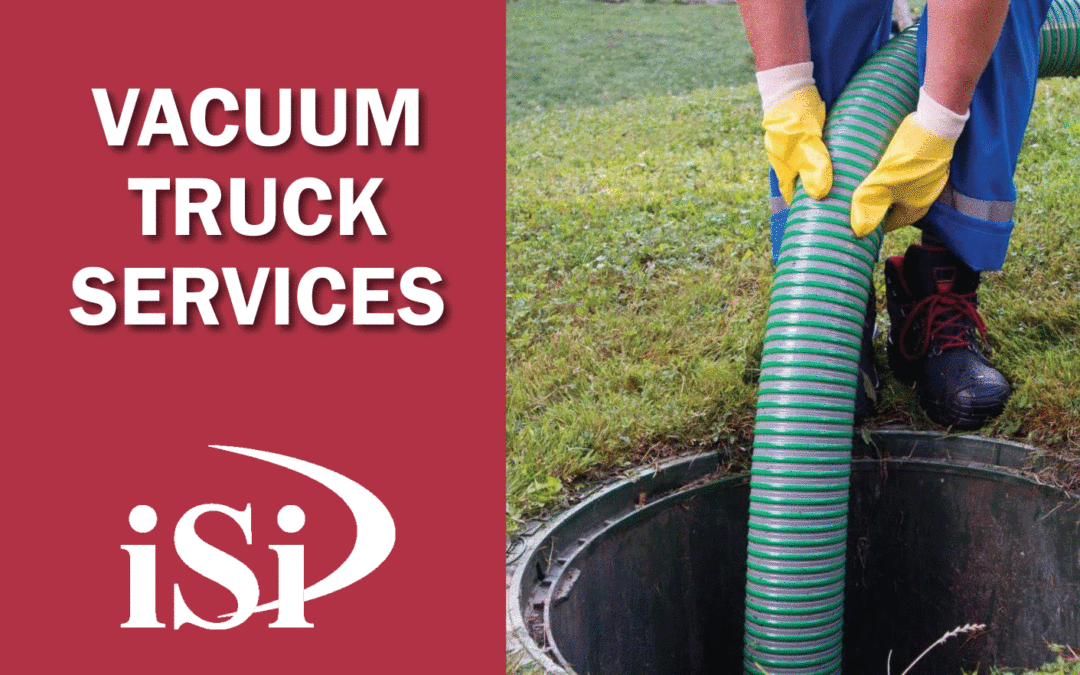
iSi Environmental – Vacuum Truck Services
Vacuum Truck Pick-up and Disposal Services for Liquids, High Solids, Oily Water and Sludge
Vacuum truck services are the perfect solution for picking up and disposing of liquids, high solids, oily water and sludge. Our team of professionals will pick-up and dispose of your waste from virtually anywhere including oil/water separators, clarifiers, sumps, trenches, pits, floor drains and even underground waste tanks.
Hydro excavation for your vacuuming needs
Hydro excavation is a safe and efficient way to excavate around utilities and other underground infrastructure. Our hydro excavation services can help you avoid the costly damage that can be caused by traditional excavation methods.
The versatile vac truck for all your waste removal needs
The versatile vac truck can be used for a variety of applications, and in many facilities, including oil/water separator cleaning, tank cleaning, pit cleaning and much more.
Contact us today to learn more about our vacuum truck services and how we can help your company with your waste removal needs.
What are vac truck services?
Vacuum truck services are a type of waste removal service that uses vacuum trucks to pick up and dispose of liquids, sludge and solids. Vacuum trucks are versatile and can be used for a variety of applications including oil/water separator cleaning, tank cleaning, pit cleaning and much more. Vac services are often paired with remediation and environmental services, are part of the formula to help facilities stay compliant with federal regulations and make certain hazardous and non hazardous waste is disposed of correctly.
How can vacuum truck services help you?
iSi Environmental’s industrial services division, named iSi Industrial Services, can help you by picking up and disposing of liquids, sludge, and solids from your property. Our team of professionals are experienced in the proper disposal of waste and can help you avoid costly damage to your property.
The different types of vacuum services include:
- Oil/water separators cleaning
- Tank cleaning
- Pit/Trenches cleaning
- Sewage disposal
- Grease trap cleaning
- Pumping of slurries and sludges
- Pump clean water
- Pumping and liquid transfer within facility
- Hazardous materials transport
- Dispose of non hazardous materials
- Tank transfer services
Why choose iSi Industrial Services?
- We offer efficient solutions to safely remove waste from your site.
- Our team of professionals are experienced and knowledgeable in the proper disposal of waste.
- 30 years of experience with local, state, and federal regulations.
- Committed to any emergency request
- iSi Industrial Services can work with your current disposal facilities locations or provide additional disposal options.
- We have the latest vacuuming technology to get the job done right. The right equipment to tackle any job (hazardous or non hazardous).
- We offer competitive pricing, a flexible schedule, from a convenient location near you. We serve the state(s) of Kansas, Oklahoma, Missouri, and Nebraska.
- Quick response time and ease of onboarding for your company
- DOT certified operators
- Fleet of well maintained transport equipment
Message us today to learn more about our vacuum truck services, request service and schedule your job today!
About iSi
iSi Industrial Services and iSi Environmental have teamed to provide environmental remediation, industrial cleaning and EHS consulting services for over 30 years. Our staff of 20+ in house consultants, combined with teams of experienced remediation crews, gives us the capability to handle unique issues that arise at any facility. Headquartered in Wichita, Kansas, our 140 employees services offices in Kansas City, Tulsa, and Atlanta. Contact us now via phone (888-264-7050) or through the website and we will put your project on the schedule.
Need Assistance?
Need vacuum truck services in Kansas, Oklahoma, Missouri or Nebraska? Contact us!