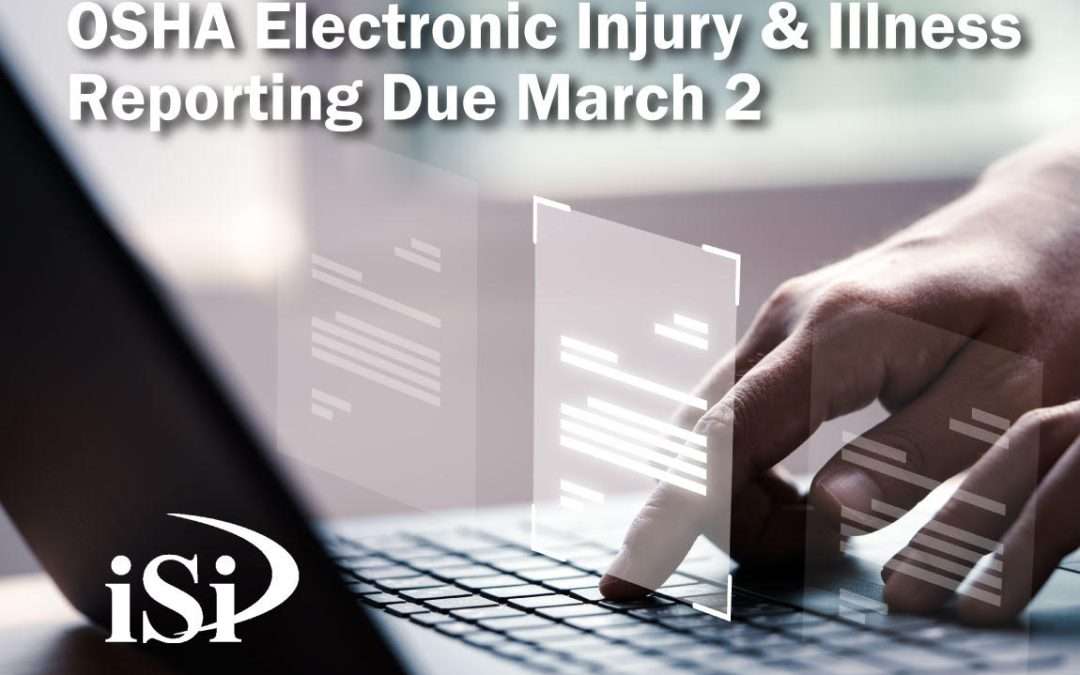
OSHA Electronic Injury and Illness Reporting Due March 2
OSHA’s final rule on electronic injury and illness reporting that passed in 2023 took effect on January 1, 2024. The new rule added some new companies and increased some of the reporting requirements. Electronic reports for 2023 injuries and illnesses are due March 2. Make sure you know what your company’s responsibilities are – do you need to report electronically?
What’s New in Electronic Reporting Standard
Companies with 20-249 employees whose NAICS codes were listed on Appendix A of the standard were required to submit their 300A electronically. This did not change, however a new appendix, Appendix B, was created for companies with 100 or more employees. This requires many more industries to report electronically. In addition to submitting the 300A, the 100+ employee companies who fall under Appendix B will also now need to submit their 300 and 301 forms.
As with 300A information, data from the 300 and 301 logs will be published on the OSHA website. Personally identifiable information from the 301, such as fields 1, 2, 6 and 7: employee name, employee address, physician name, and treatment facility name and address will not be collected.
The rules did not change for all companies with 250 or more employees. All companies, regardless of NAICS code, will need to submit their 300A forms. Those with 19 or fewer employees will still not be required to report.
Another change includes making inclusion of your company’s legal name required. Previously, only the Tax Identification number was required.
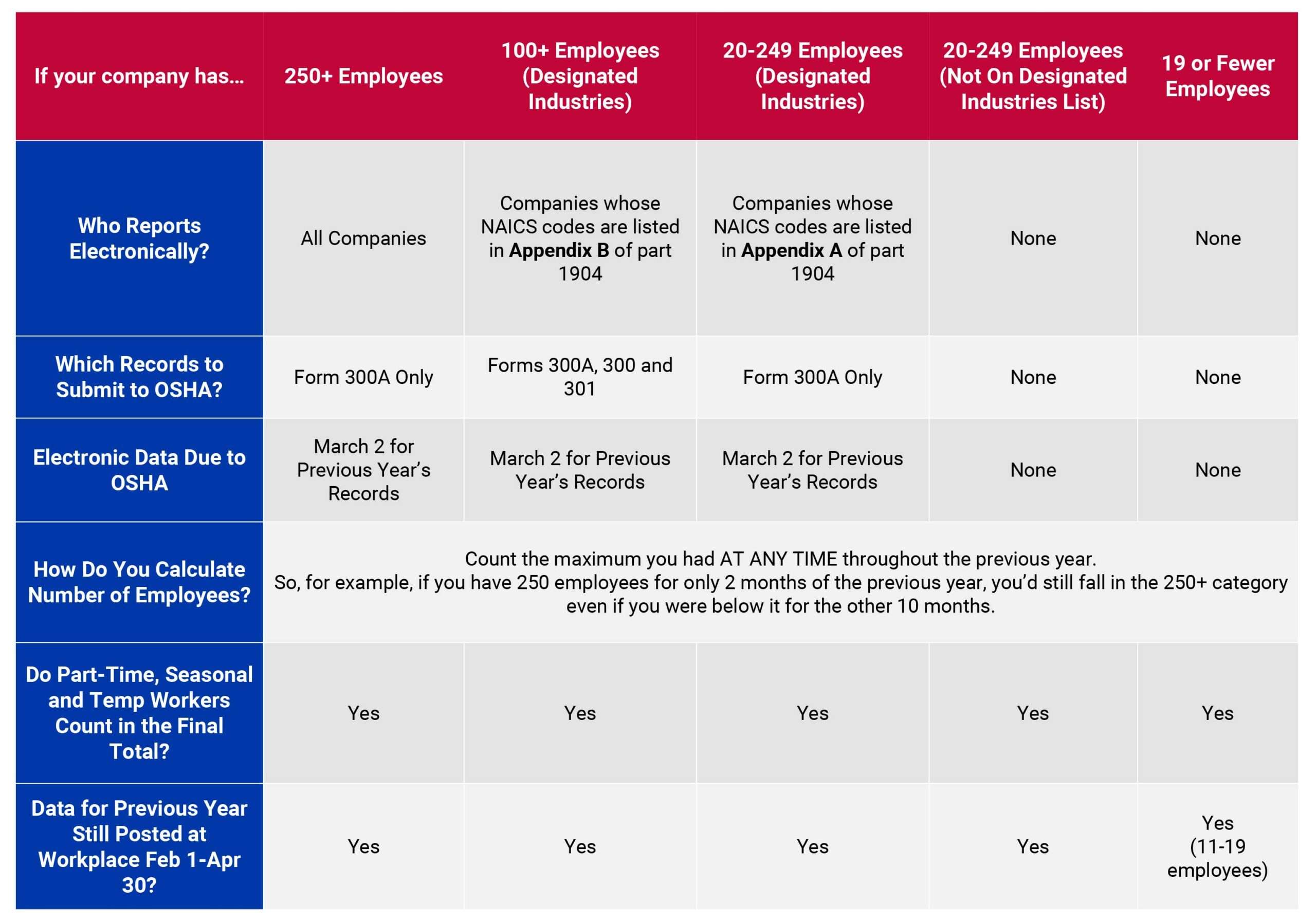
Industries Moved from Appendix A to Appendix B
Some NAICS codes were moved from Appendix A to Appendix B due to increased fatalities or increases in DART (Days Away; Restricted; Transfer) rates. Those companies with 20-249 employees who had been submitting only the 300A are now required to submit the 300 and 301. These include:
- NAICS 1133-Logging
- NAICS 1142-Hunting and Trapping
- NAICS 3379-Other Furniture Related Product Manufacturing
- NAICS 4239-Miscellaneous Durable Goods Merchant Wholesalers
- NAICS 4853-Taxi and Limousine Service
- NAICS 4889-Other Support Activities for Transportation
Why They Are Requiring the 300 and 301 Log for Some Industries?
Besides finding additional industry data on increased injuries, DART rate and fatalities, OSHA’s intent is to collect more accurate and detailed information for injuries and illnesses to help ultimately make workplaces safer. The detailed information is meant to help make statistics more accurate and to help identify trends that are relevant to industries and types of workers. The only time OSHA was able to get detailed information was through inspections. The type of data they will be gathering allows for different kinds of statistical analyses and to help determine where initiatives are successful, are failing, or need to be developed.
OSHA sees gathering 300 and 301 information as a benefit not only to themselves, but by posting it online it can be beneficial information to industries, employers, employees, safety consultants like iSi, and to the general public.
Some examples of this that they used in their final rule document include:
- 300A information only tells how many of each type of incident on that form are occurring. Now they will be able to see the different kinds of injuries and what they are. For example, “respiratory conditions” could mean as a result of chemical exposure, COVID, TB, or Legionnaires.
- Now data can be pulled by roles within any type of company. For example, injuries for nurses aides vs. nurses vs. doctors in medical facilities.
- The Presidential directive on climate change has OSHA them focused on heat hazards. The new information will help them figure out what kinds of injuries and illnesses are attributed to heat.
- This will help give employers another resource to consult besides industry groups and insurance to benchmark themselves against others in their industry. For example, the state of Michigan independently researched and found that bath refinishing contractors had 13 deaths in the span of 12 yrs. From that information, they found it was because of the chemical strippers that were being used. As a result, safety guidance and training was sent to those companies to help improve safety and to alert them of those hazards in order to reduce the deaths.
- Another employer in New York researched all injuries from their multiple worksites and found that there had been 11,000 lost workdays because of ladders. To reduce those numbers, they increased training in that area, making injuries drop to close to none. With publicly available information, research like that can be done by multiple parties to help find ways to strengthen workplace safety.
Need Advice?
If you need help navigating this standard, or have questions about it, contact us today!
Need Help?
Need an extra hand to get your safety issues covered? How about policies/programs developed or training conducted?