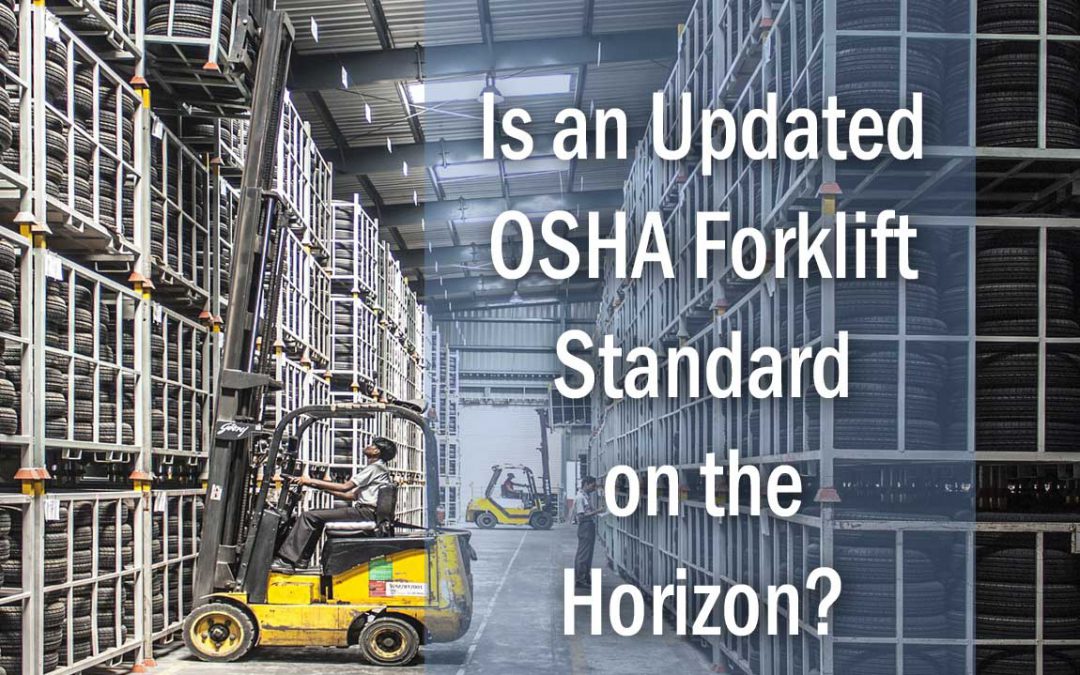
Is an OSHA Updated Forklift Standard on the Horizon?
OSHA is soliciting information on powered industrial vehicles to determine the need for an updated standard. The current standard was written in 1971, based on industry data from 1969. OSHA realizes that national consensus standards have been updated several times and rule updates may be needed.
The term “powered industrial vehicle” refers to forklifts, fork and lift trucks, tractors, motorized hand trucks and other specialized industrial trucks that have an electrical or combustion engine.
OSHA is requesting information on:
- Types, Age and Usage of Powered Industrial Vehicles in the Workplace
- Maintenance and Retrofitting
- How to Regulate Older Trucks
- Types of Accidents and Injuries in Operating
- Costs and Benefit of Retrofitting With Safety Features
The agency is accepting comments electronically until June 10, 2019 at regulations.gov and from there, OSHA will be making a determination of what actions, if any, needs to be taken.
Powered industrial vehicle incidents are among OSHA’s Top 10 each year, and a number of OSHA regions currently have emphasis programs dedicated to them as well. Emphasis programs dictate that if an inspector sees a powered industrial vehicle while onsite for any other issue, the inspector can automatically include your powered industrial vehicles in the scope of the inspection.
There are a number of common regulatory issues with powered industrial vehicles, mainly forklifts, that you need to be aware of to ensure compliance before your next inspection. Check out our previous blog article, Forklift Top 6: Common OSHA Compliance Pitfalls for Powered Industrial Trucks
Are Your Forklifts Compliant?
Many OSHA regional emphasis programs include forklifts. Is your program compliant and ready for inspection? Let us help!