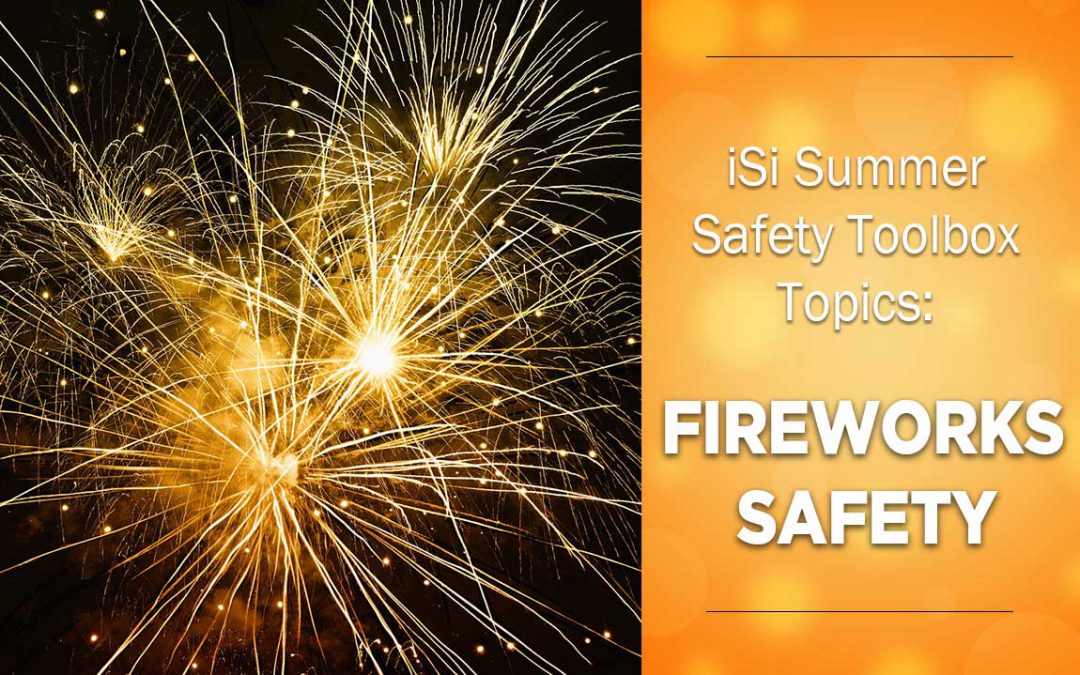
iSi Summer Toolbox Topics: Fireworks Safety
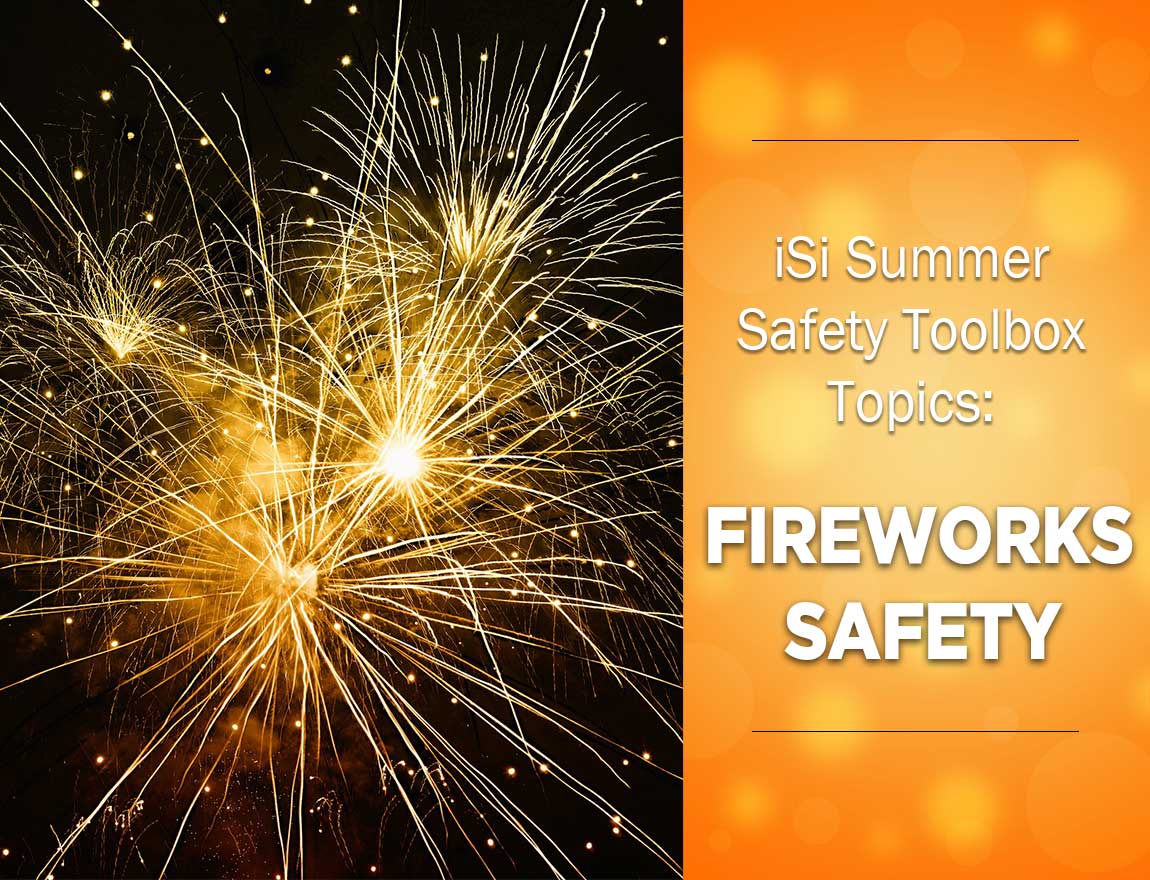
One of the favorite events of the 4th of July holiday for many people is shooting fireworks. Contrary to what we may have seen and done in our teenage years, fireworks can actually be pretty dangerous. Here are some tips to remember and share for a safe holiday:
- Know your local laws regarding the use of fireworks such as where you are allowed to shoot them, which types are not allowed and at what times you can shoot them.
- If you’re not allowed to shoot them in your home area and need to go across city or county lines, make sure you have the permission of the owner of where you’re going to shoot them.
The Setup
- Always use fireworks OUTSIDE within a clear area. Stay way from buildings and vehicles.
- Stay away from trees, bushes, and other dry vegetation.
- Adults should supervise all firework activities.
- Alcohol and fireworks do not mix. Save your alcohol for after the show.
- Always have a bucket of water and a water hose nearby.
Shooting the Fireworks
- Before you begin, know your fireworks: read the caution labels and performance descriptions before igniting.
- Wear safety glasses when shooting fireworks.
- Light one firework at a time and then quickly move away.
- Sparklers look harmless, but they can burn at 2000 degrees and quickly ignite clothing. Make sure anyone using them has their shoes on and that they hold them out away from their clothes and skin.
- Never relight a “dud” firework. Wait 20 minutes and then soak it in a bucket of water.
- Never carry fireworks in your POCKET or shoot them into METAL or GLASS containers.
- Old fireworks can be a safety hazard—make sure they haven’t gotten wet and that the fuse is intact before using.
Disposal
- Smoldering fireworks can cause a fire in a trash can.
- Soak used and dud fireworks in a bucket of water for at least 20 minutes, or overnight which is even better.
- If you find old fireworks that are damaged or you don’t want to light them, don’t just throw them away. Soak them in a bucket of water until fully wet.
- Wrap the wet fireworks in Ziploc bags, trash bags or plastic wrap so they won’t dry out—especially the unused ones that still contain the explosives within them. Dry fireworks can become unstable.
Fireworks and Pets
- Don’t bring your pets to a fireworks display, even a small one.
- If fireworks are being used near your home, put your pet in a safe, interior room to avoid exposure to the sound.
- Treat toys filled with their favorites such as pumpkin, peanut butter or applesauce may be a good distraction to keep their minds busy.
- Make sure your pet has an identification tag, in case it runs off during a fireworks display.
We hope you have a safe and wonderful Independence Day holiday!
.One of the favorite events of the 4th of July holiday for many people is shooting fireworks. Contrary to what we may have seen and done in our teenage years, fireworks can actually be pretty dangerous. Here are some tips to remember and share for a safe holiday:
- Know your local laws regarding the use of fireworks such as where you are allowed to shoot them, which types are not allowed and at what times you can shoot them.
- If you’re not allowed to shoot them in your home area and need to go across city or county lines, make sure you have the permission of the owner of where you’re going to shoot them.
The Setup
- Always use fireworks OUTSIDE within a clear area. Stay way from buildings and vehicles.
- Stay away from trees, bushes, and other dry vegetation.
- Adults should supervise all firework activities.
- Alcohol and fireworks do not mix. Save your alcohol for after the show.
- Always have a bucket of water and a water hose nearby.
Shooting the Fireworks
- Before you begin, know your fireworks: read the caution labels and performance descriptions before igniting.
- Wear safety glasses when shooting fireworks.
- Light one firework at a time and then quickly move away.
- Sparklers look harmless, but they can burn at 2000 degrees and quickly ignite clothing. Make sure anyone using them has their shoes on and that they hold them out away from their clothes and skin.
- Never relight a “dud” firework. Wait 20 minutes and then soak it in a bucket of water.
- Never carry fireworks in your POCKET or shoot them into METAL or GLASS containers.
- Old fireworks can be a safety hazard—make sure they haven’t gotten wet and that the fuse is intact before using.
Disposal
- Smoldering fireworks can cause a fire in a trash can.
- Soak used and dud fireworks in a bucket of water for at least 20 minutes, or overnight which is even better.
- If you find old fireworks that are damaged or you don’t want to light them, don’t just throw them away. Soak them in a bucket of water until fully wet.
- Wrap the wet fireworks in Ziploc bags, trash bags or plastic wrap so they won’t dry out—especially the unused ones that still contain the explosives within them. Dry fireworks can become unstable.
Fireworks and Pets
- Don’t bring your pets to a fireworks display, even a small one.
- If fireworks are being used near your home, put your pet in a safe, interior room to avoid exposure to the sound.
- Treat toys filled with their favorites such as pumpkin, peanut butter or applesauce may be a good distraction to keep their minds busy.
- Make sure your pet has an identification tag, in case it runs off during a fireworks display.
We hope you have a safe and wonderful Independence Day holiday!