
Recognize the Signs of Heat Illness
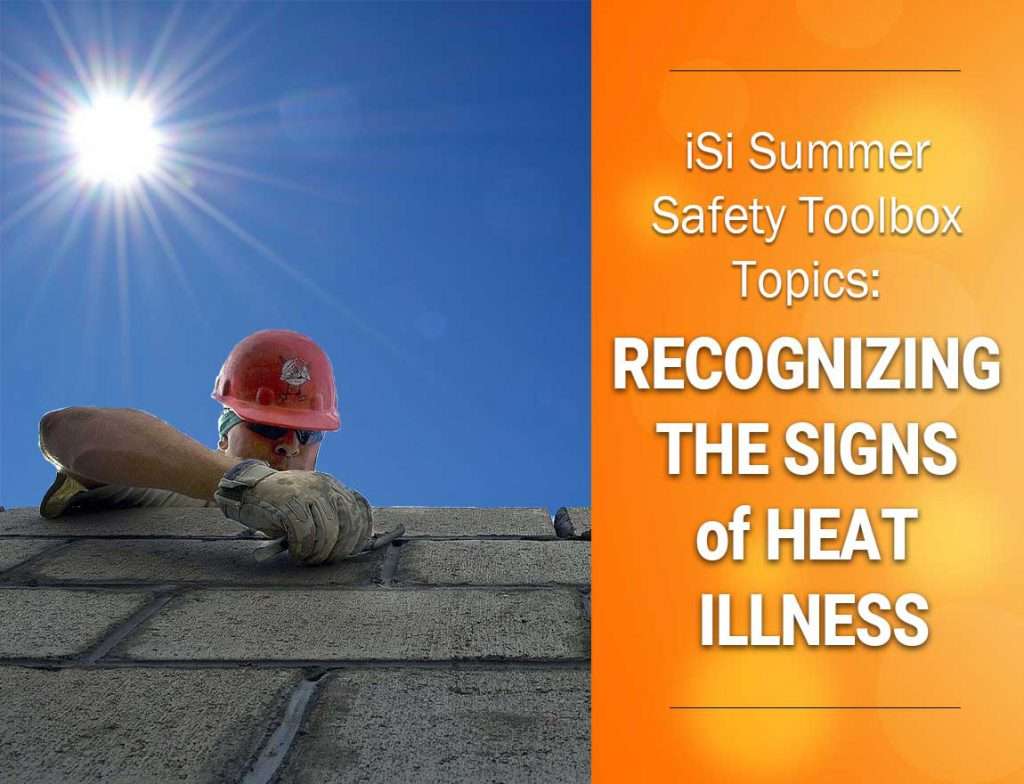
Hot working conditions can bring increased risks of heat illness, especially when heat-producing equipment is used.
OSHA has added an item in its Spring Regulatory Agenda called “Heat Illness Prevention in Outdoor and Indoor Work Settings” to start the wheels in motion for a potential heat-related regulation. Right now it’s only in the Request for Information stage, but congressional members and public citizens have been petitioning for a standard for a while. Some state plan states have already included heat-related rules in their standards.
Heat is the leading weather-related killer. The most important thing to remember about a person suffering from heat illness is to get them out of the heat ASAP. Take them to a shaded or air-conditioned area. A running vehicle with air conditioning works if no shaded area is available. Always stay with a victim of heat illness until medical personnel arrive. Be aware of yourself and your team for any symptoms and take the appropriate action immediately.
Heat rash can appear on skin as small or large clusters of red bumps.
- What to do:
- Get to a cool, dry place.
- Keep rash dry; use powder to soothe.
Heat cramps bring pain or spasms to muscles.
- What to do:
- Halt physical activity until cramps go away.
- Get to a cool place.
- Drink water or electrolyte drink.
- Seek medical attention if the victim:
- Has cramps lasting longer than 1 hour.
- Has heart problems.
- Is on a low-sodium diet.
Heat exhaustion occurs when the body’s temperature can’t cool down. Think of this as a situation where extreme conditions exhaust the body. It is severe and can occur in one day or over multiple days when in a consistently hot environment.
- Watch for:
- Heavy sweating
- Cold, clammy, pale skin
- Fast and weak pulse
- Nausea or vomiting
- Headache
- Weakness or tiredness
- Dizziness
- Fainting
- Muscle cramps
- What to do:
- Get to a cool place.
- Loosen clothing.
- Sip water; do not chug.
- Place cool cloths or cold packs under arms or on neck.
- Seek medical attention if the victim:
- Is vomiting.
- Experiences worsening symptoms.
- Experiences symptoms lasting longer than 1 hour.
Heat stroke occurs when body temperature is excessively high. Think of this as a situation that causes the body to stroke or seize up completely. This is a serious medical emergency that can cause shock, brain damage, organ failure, and death. It could be caused by heat exhaustion that was not properly treated.
- Watch for:
- Red, hot, dry skin (no sweating)
- Fast and strong pulse
- Nausea
- Throbbing headache
- High body temperature
- Dizziness or confusion
- Slurred speech
- Losing consciousness
- Seizures
- What to do:
- Call 911 – follow their advice.
- Get to a cool place.
- Loosen clothing.
- Place cool cloths or cold packs under arms or on neck.
- Do not provide anything to drink.
Dehydration can be a common cause of heat illness. Maintaining hydration is important, even if you don’t feel thirsty. Drinking water or electrolyte drinks are highly preferred to sugary and heavily caffeinated drinks. OSHA recommends drinking small amounts of cool water often before getting thirsty; 4 cups every hour during heat index values between 103°F – 115°F. Another recommendation is not to exceed 12 quarts of water per day.
An important reminder is that every person and situation is different. Some people require more water than others. These intake amounts depend on several things including the type of work being done, how much you’re sweating, and your personal risk factors. Don’t chug a large amount of water in the morning and call it good for the day; the important thing is maintaining hydration. You don’t flood your vegetable garden once at the beginning of the month and neglect it the rest of the month. If you do, you probably don’t have much of a harvest.
It’s the supervisor’s duty to have a plan in place during days of extreme heat. If possible, rescheduling a job to a cooler day or even a cooler part of the day could make a difference. Getting a job done on time is important, as is maintaining client satisfaction. However, no part of a job is worth risking the health and safety of your team and clients should understand that.
OSHA Heat Regulation
Monitor OSHA’s progress on a potential heat illness prevention standard here.


Contributing:
Drew Lyon
Project Manager | Meteorologist
Drew Lyon’s experience and training encompasses environmental reporting, day-to-day EHS compliance assistance at manufacturing facilities, wastewater compliance, hazardous waste management, environmental field sampling and safety. She is also a meteorologist, providing weather-related guidance to clients and our team.