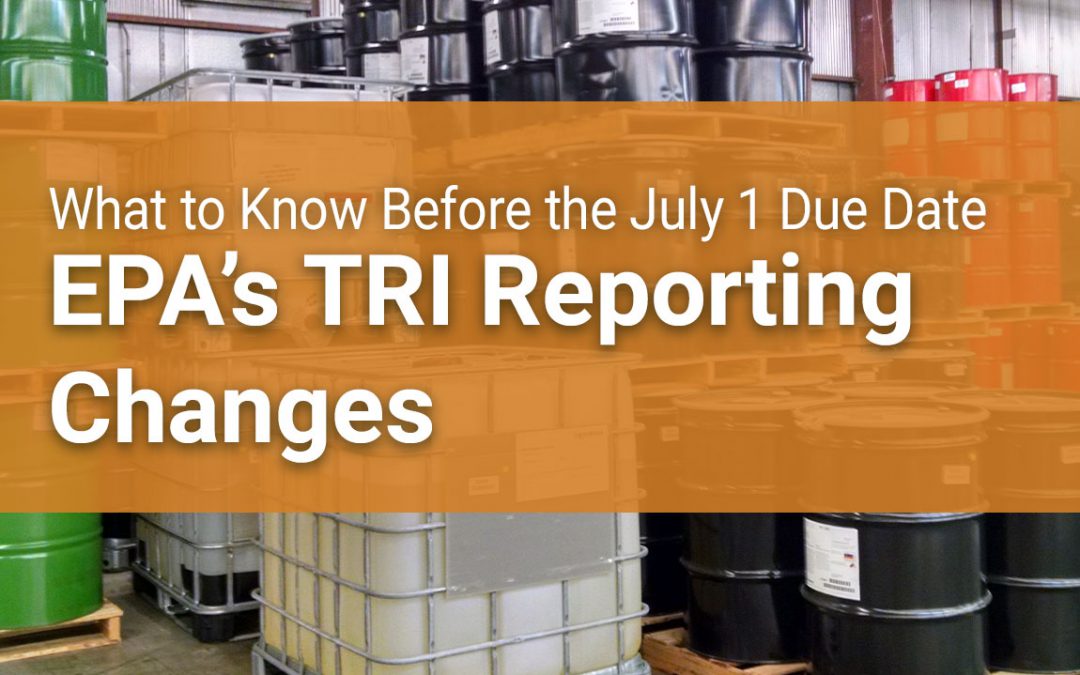
EPA’s Changes to TRI Reporting: What to Know Before the July 1 Due Date
EPA has made some updates, changes and additions to their Toxic Release Inventory (TRI) reporting. Their focus on environmental justice is evident in many of these changes.
Because the TRI is used as a mechanism to publicly report businesses’ chemical and release information, changes and additions to the TRI is a logical place to start when it comes to EJ’s goal of transparency and giving citizens equal access to information to make decisions on where they live and work. Thus, this is an easy place to start, and where we may find more changes throughout the year.
TRI reports, aka Form R, also aka SARA 313 reports are due July 1.
What’s Environmental Justice?
EPA defines EJ as:
“The fair treatment and meaningful involvement of all people regardless of race, color, national origin, or income, with respect to the development, implementation, and enforcement of environmental laws, regulations, and policies. This goal will be achieved when everyone enjoys:
- The same degree of protection from environmental and health hazards, and
- Equal access to the decision-making process to have a healthy environment in which to live, learn, and work.”
EPA has an entire section dedicated to EJ on its website. They even have a mapping and search tool called EJSCREEN that combines environmental and demographic indicators in maps and reports.
Changes in Some de Minimis Percentages
EPCRA Section 313 and chemical categories are subject to a 1% de minimis concentration unless the substance has been named a carcinogen or potential carcinogen. That is, when you’re determining thresholds of chemicals, some chemicals can be exempt from reporting if you have minimal concentrations of non-Persistent Bioaccumulative Toxic (PBT) chemicals in mixtures. This is called a de minimis exemption. The following chemicals have had their de minimis percentages altered from 1% to 0.1% because they are now OSHA carcinogens:
Reporting Year 2020 (due July 1, 2021)
- Pyridine
- Methyl acrylate
- Quinoline
- Vinylidene chloride
Were Changed for Reporting Year 2019 (due last year)
- N,N dimethylformamide (CAS 62-12-2)
- 2-mercaptobenzothiazole (CAS 149-30-4)
- Molybdenum trioxide (CAS 1313-27-5)
Supplier Notifications
Don’t forget that companies who process or manufacture TRI-listed chemicals or chemical mixtures are required to send annual supplier chemical notifications per EPCRA Section 313. For more details on who and what that entails, check out our blog “Annual Supplier Notifications: Does This Affect Your Company“?
Per- and Polyfluoroalkyl Substances (PFAS) Reporting
The 2020 National Defense Authorization Act requires a PFAS to be added to TRI when it meets a certain criteria. For reporting year 2020, EPA added 172 PFAS chemicals. The threshold for those is 100 pounds, manufactured, processed or otherwise used. If you use any of these chemicals, these should be included in your reporting year 2020 reports, due July 1, 2021.
For the 172 PFAS chemicals, the de minimis concentration for perfluorooctanoic acid (PFOA) is 0.1%. For all other PFAS chemicals, the de minimis level is 1%.
So far for the 2021 reporting year, EPA has added three new PFAS: perfluorooctyl iodide, potassium perfluorooctanoate and silver(I) perfluorooctanoate. These also have the same threshold of 100 pounds. EPA will be adding more as they come along. EPA is anticipating that perfluorobutane sulfonic acid (PFBS) will be the next one added.
For more information about the 172 PFAS chemicals, go to EPA’s site here. For guidance on PFAS reporting, you can visit the special PFAS guidance here.
PFAS Fire Suppression Foam
Fire suppression aqueous film forming foam (AFFF) is a common PFAS chemical.
For this chemical, if it is released for system testing, training or to suppress a fire, it’s considered otherwise use and needs to be reported on your TRI.
If it’s not used onsite, but just stored there, it’s not considered an activity and does not need to be reported. Only when it’s released from a fire suppression system is it considered an activity (that is, manufacture, process or otherwise).
If you use the fire foam offsite it’s not included in the threshold.
TSCA Work Plan and High-Priority Chemicals
EPA would like to add chemicals that are listed on the Toxic Substances Control Act’s (TSCA) Work Plan. The TSCA Work Plan is a list of 90 chemicals under further assessment by EPA. Those chemicals are chosen based on their potential for high hazard and exposure. As an example, the first 10 of those 90 chemicals currently under review include:
- 1,4-Dioxane
- 1-Bromopropane
- Asbestos
- Carbon Tetrachloride
- Cyclic Aliphatic Bromide Cluster
- Methylene Chloride
- N-methylpyrrolidone
- Pigment Violet 29
- Tetrachloroethylene, aka Perchloroethylene
- Trichloroethylene
EPA would also like to take a look at adding other chemicals from a list of 25 chemicals suggested for addition by the Toxics Reduction Institute in Massachusetts. The group petitioned EPA to add 25 more chemicals to TRI. EPA is evaluating those to determine if they meet the EPCRA 313(d)(2) criteria. Some examples of these include:
- 1, 2, 3-Trichlorobenzene
- 1,3-Dichloro-2-propanol
- n-Propyl Bromide (1-Bromopropane)
- Formamide
- 1,1’-Azobis (Formamide)
- Nitrilotriacetic Acid, Trisodium Salt
- N, Ndimethylacetamide
- Hexahydrophthalic Anhydride
Facilities Added to TRI Reporting Requirements
Natural Gas Processing Facilities
Natural gas facilities will be an included type of facility on the Emergency Planning and Community Right to Know Act (EPCRA) Section 313. Thus, those facilities will need to submit reports to TRI. EPA wants to make sure natural gas processors’ chemical releases and waste management activities with TRI-listed chemicals are available to the public because millions of people live within 30 miles of at least one natural gas processing facility.
Contract Sterilization Facilities
Further reporting of ethylene oxide (EtO) will be required on the TRI. Specifically, contract sterilization facilities have been called out as types of facilities this will affect. EtO is used to sterilize medical devices and to make certain chemicals. Contract sterilization facilities currently are not required to report, but they will be required in the future. EPA says that these facilities often are located in areas with environmental justice issues, affecting those who work there and live around them. Adding these facilities to the list will give more information about EtO releases and allow EPA to respond to the health and environmental threats they cause.
Adding More TRI Tools for the Public
EPA wants to make TRI data even more useful and accessible for the public. As a result, they want to make the following additions:
- Add a demographic profile section to TRI so that you can search by income profile and race, similar to what’s available on EJSCREEN;
- Launch a Spanish version of the TRI; and,
- Promote the Pollution Prevention (P2) information that companies are required to include in their TRI reports. EPA hopes that this will encourage the community to work with the TRI facilities to increase their P2 efforts and reduce releases in the community.
There are currently no timetables for completion of these new goals and additions. iSi will keep you updated as we see changes and additions finalized and added to TRI or EPCRA.


Contributing:
Amanda Scheufler, CHMM
Consulting Services Director
Amanda’s experience and training encompasses all things environmental compliance and environmental auditing. Her specialties include environmental reporting, hazardous waste management, air compliance, Storm Water Pollution Prevention, SPCC, and Facility Response Plans. Managing iSi's Consulting Services division, Amanda has served as an onsite safety and environmental manager for several industrial facilities through iSi's EHS COOP program and she also teaches part of iSi's Hazardous Waste Management class.