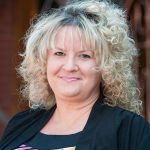
About the Author: Tami Hadley, iSi’s Marketing Director, has been involved in numerous professional organizations as a member and leader and has served on conference planning committees for over 23 years.
Fall is a busy time for iSi as there are a number of environmental, health and safety (EHS) conferences and professional organizations we’re involved in. At a recent conference, I was reminded how important getting out to these events can be to an EHS professional’s job.
Although EHS professional groups and conferences have one big difference, that being the frequency in which they are held, they are quite similar in their advantages.
Stay Current on Regulations
Although you may subscribe to the Federal Register, blogs and newsletters, how often do you read them? Are you looking at all of them all the time? Do your sources encompass all aspects of EHS compliance that your company is required to follow?
It’s super easy to miss something. Professional groups and conferences allow you direct access to new information and discussion about upcoming regulations. Often the regulators themselves will be the speakers and will give you some extra insight into new regulations, what has changed and why, what’s on the horizon, and what the compliance nuances are. The regulators are also there to answer your questions.
Meet People Who Have the Same Issues You Do
One of the most valuable things about conferences and meetings are the people you’ll meet. At your company you may be the only person responsible for EHS, and perhaps that can be a lonely feeling sometimes. However, you are not alone. There others in your area who are in the same boat as you are. They can help and give you advice.
Besides commiserating with you, they can give you ideas on how to solve issues, can tell you what works for them, and who the good vendors are. I’ve seen people share templates and programs with each other, visit each other’s facilities, discuss what’s working for them, and share training classes with each other.
Connecting and Recruiting
Making connections can be very valuable. One of the number one keys to making a connection is bringing value and sharing value because what you are able to give often comes back to you multiple times over. Goodwill begets goodwill. The people that you meet can introduce you to people they know who may be able to give you information or recommend a solution or a vendor. It’s the old adage, it’s not what you know but who you know.
Are you looking for good employees to help you at your facility? These events are great for determining potential candidates and seeing who the most respected and knowledgeable professionals in the area are. You may not need someone now, but having an idea of who is in the area and having them know you will save you a ton of time later. Conversely, it’s a chance for you to highlight your expertise as well. If you are new to the industry or to your job, a group like this can expose you to a lot of different topics and help you learn a lot of things you may not get otherwise.
Unplugging is a Good Thing
Besides the list of tasks we’re expected to accomplish each day, we are inundated by phone calls, emails, texts, persons coming by, fires to put out, etc. The day-to-day grind can really get in the way of continuing education. How many times have you been in a training class at your site and have gotten pulled out for some reason, or have been watching a webinar at your desk only to get interrupted by someone coming in your office or calling you?
Getting offsite for a day or two, or even for a lunch or a breakfast, sets aside a time for you to get your focus back onto learning something new. Even if the speaker doesn’t teach you something new, the time away to immerse yourself in the topic may jolt some new ideas because you’ve had the time to unplug from the clutter and focus on the topic at hand.
It’s OK to Sit by a Vendor
Don’t discount the value of vendors and suppliers. Sure, it’s most likely they are there to make connections, but these people can be some of your biggest sources of information and intelligence in all things EHS. Vendors and suppliers will often have some of the latest and greatest in compliance technologies, methods, best practices, products, apps, etc. You may not need them now, but having them there gives you an idea of who you can call when you need something.
Vendors can also tell you a lot about what companies like yours are doing, how problems have been solved by others and what is going on in the industry. It’s also their job to know who the EHS people are in your area and so they can also be great connectors for you. They go to a variety of events, so you may learn about other specialty groups and conferences and opportunities you didn’t already know about.
List of Organizations
I want to be a valuable connection for you, so below is a list of professional organizations which focus on EHS issues and may have chapters in your area. In addition to these organizations, look for other local groups in your area which are not affiliated with national chapters. There are a lot of them out there.
For conferences, I’ve seen that almost every state has a safety conference and an environmental conference. Sometimes they are combined or sometimes they are conducted within other conferences.
I can give you some specific ideas for groups and events in and around the areas in which iSi has offices: Kansas (state of Kansas and Kansas City area), Oklahoma, Georgia and surrounding states. Contact me and let me know which area(s) you’re interested in and I’ll get back with you with some ideas. In the meantime, here are some national organizations with chapters all across the U.S.:
American Society of Safety Professionals (ASSP)
American Industrial Hygiene Association (AIHA)
Alliance of Hazardous Materials Professionals (AHMP)
National Safety Council (NSC)
Air and Waste Management Association (AWMA)
Which national EHS organizations am I missing? Let me know and I’ll add them to this article!