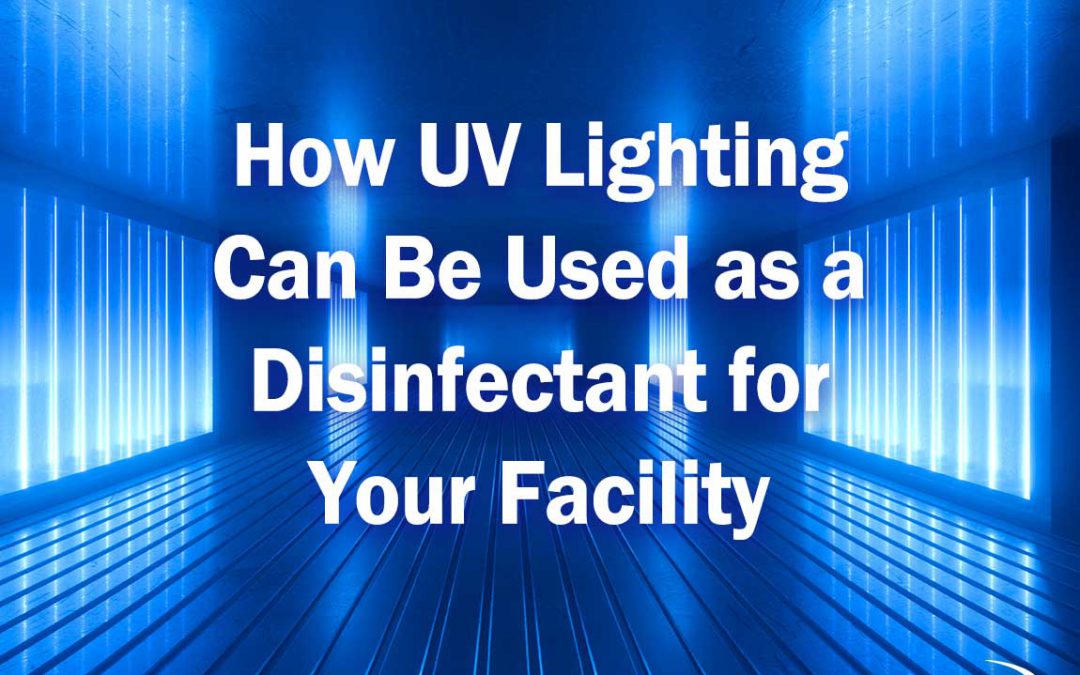
How UV Lighting Can be Used as a Disinfectant for Your Facility
UV Light for Your HVAC
iSi can now provide disinfecting UV lighting for your HVAC system. UV light installations kill protein encased viruses, bacteria and mold.
What is UVGI?
Ultraviolet Germicidal Irradiation, or UVGI, is a technology that goes back to the 1930’s with studies showing that ultraviolet light has the ability to kill or inactivate airborne microorganisms. These studies showed that an optimal wavelength of 265 nanometers (nm) was able to provide the largest reduction in airborne microorganisms. This was found to be very close to the wavelength produced by low-pressure mercury vapor lamps (254 nm).
Ultraviolet light can be broken down into 4 different bands:
- UV-V: 10-200 nm
- UV-C: 200-280 nm
- UV-B: 280-315 nm
- UV-A: 315-400 nm
The sun emits the full spectrum of ultraviolet light but only UV-A & UV-B make it to the surface. The others are filtered out by the Earth’s atmosphere. The UV-C band is the most effective at attacking the harmful microorganisms, so it needs to be generated artificially.
How does UVGI work?
UV-C wavelengths are readily absorbed by the DNA and RNA of microorganisms such as germs and mold. When absorbed, UV damages their DNA or RNA structure, preventing the microorganism from replicating. The magnitude of their reduction is affected by their resistance to UVGI, the quantity of UV energy delivered, and the type specific microorganism being irradiated.
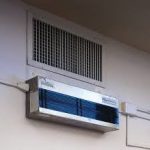
Wall-mounted UV light system.
Disinfecting light is delivered in two common methods. The first is by placing light units, either with or without fans, near the top of a room close to the air vents in order to clean the air as it circulates the room.
The second method is to place the unit directly into the heating and air conditioning (HVAC) system. This second method places the light in a location where the room occupants are not directly exposed to the light, and if placed correctly, can have an added advantage of cleaning the HVAC coils and drip pan to improve the efficiency of the HVAC system.
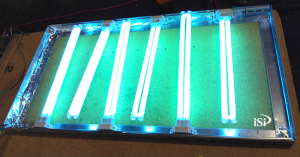
UV light for HVAC system.
The design and placement of these different systems are governed by the American Society of Heating, Refrigerating, and Air-Conditioning Engineers (ASHRAE) which has published many documents on the subject.
UV Safety Considerations
UV-C band light is a safer band than the UV-A and UV-B that we deal with in nature. We have always been taught to apply sunscreen and wear sunglasses to protect ourselves from the burns we receive when outside. Due to the shorter wavelengths UV-C will only penetrate the outer skin layers and along the surface of the eye. It will not give you the severe sun burn the longer wavelengths will. It will cause a reddening and slight irritation of the skin and an painful itching sensation that will last a few days in the eye so slight protection is required if you are directly exposed to the light from these units.
UV Lighting for Your HVAC Units
iSi is now providing the second method UV germicidal lighting, the one for your HVAC system. Our units are customized to your specific HVAC system and area to be disinfected. Learn more about this service and get a quote here.


Contributing:
Ryan Livengood
International Hazardous Materials Logistics Manager | EHS Regulatory Trainer
As a former corporate environmental, health and safety manager, Ryan has a vast experience in working with both environmental and safety compliance issues in multiple states. His specialties include national and international dangerous goods transportation, hazardous waste, environmental compliance, industrial hygiene and safety compliance. He is also an ISO 14001 Lead Auditor.