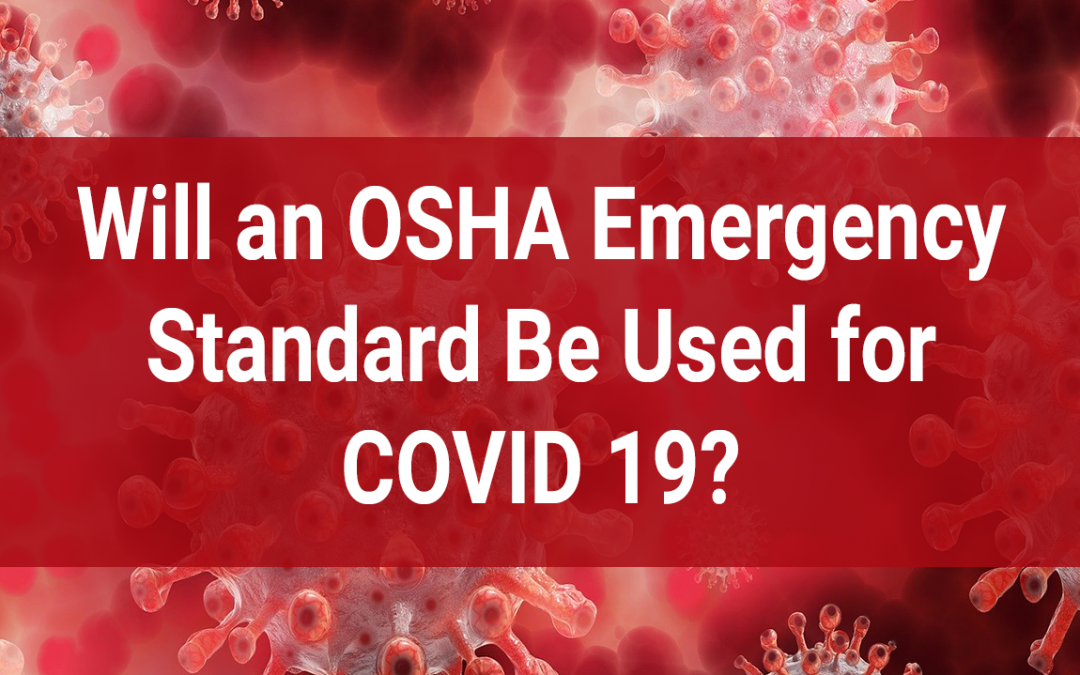
Potential Employer Requirements in an OSHA Emergency Standard for COVID
UPDATE:
President Biden signed an Executive Order on Thursday, Jan. 21, 2021 that requires the following:
- Within 2 weeks (by Feb. 4, 2021), OSHA is required to:
- Issue guidance to employers on workplace safety during the COVID pandemic.
- OSHA and MSHA are required to determine if an emergency temporary standard is necessary. If so, it will be due by Mar. 15, 2021.
- OSHA is required to review its enforcement efforts and identify any short-term and long-term changes to be made.
- A National Emphasis Program on COVID-19 in the workplace is required to be developed.
- OSHA is to work with state plan states to make sure they have similar COVID plans in place, and for those who don’t have a state plan, work with state and local officials to make sure they have plans in place to protect public employees.
- The Secretaries of Labor, Health and Human Services, Transportation, Energy and Agriculture need to work to identify that workers not covered under OSHA in their respective categories are protected.
What’s an OSHA Emergency Temporary Standard?
Under certain limited conditions, OSHA is authorized to set emergency temporary standards that take effect immediately and are in effect until superseded by a permanent standard. OSHA must determine that workers are in grave danger due to exposure to toxic substances, new hazards, or agents determined to be toxic or physically harmful where an emergency standard is needed to protect them. OSHA publishes the emergency temporary standard in the Federal Register, where it also serves as a proposed permanent standard. It’s subject to the usual procedure for adopting a permanent standard except that a final ruling should be made within six months. The validity of an emergency temporary standard may be challenged in an appropriate U.S. Court of Appeals.
What May Employers Be Required to Develop in a Federal Standard?
In total, 14 states have adopted comprehensive COVID-19 worker protections through executive order and/or their state OSHA programs.
Currently, there are 4 states – California, Virginia, Michigan and Oregon – that have issued a state-specific OSHA emergency standards through their state plans. There are common themes between the policies of these 4 states and they have pulled items from each other. These items would likely become a part of a federal emergency standard:
Conducting a Workplace Assessment
This would include identifying employee tasks, work environment, presence of the virus, number of employees, facility size, working distances, duration and frequency of exposure, and hazards encountered.
Develop an Exposure Control Plan
This would include designating an on-site COVID coordinator, providing free face coverings and requiring their use, signage, social distancing, barriers, remote working, prohibiting sick employees access to facility, enhanced cleanings for positive cases, employee screenings, and notification of positive cases.
Implement Controls
This includes maximizing current ventilation systems, installing barriers, partitions, and airborne infection isolation rooms.
Training Employees
Training would need to be specific to the place of employment. Included would be reviewing control measures, proper use of PPE, how to report symptoms or positive cases, how to report unsafe working conditions, and an overview of the COVID-19 virus, symptoms, and means of transmission.
Maintain Records of Training, Screenings, and Notifications
This would include employee training, employee and visitor screenings, notifications as required to individuals and Health Departments.
How Often Have Emergency Standards Been Used Before?
OSHA has used emergency temporary standards 9 times. The last time they were used was in 1983 for asbestos. OSHA’s first emergency standard was also created for asbestos, and others have been created mostly for chemicals, including 12 different carcinogens, benzene and vinyl chloride. Most standards have been challenged in court, and although there have been a few that have been vacated, most have remained in place.
###
iSi will be monitoring developments with federal OSHA and will update this article, or provide additional information in our blog as information continues to develop regarding this issue.
We're Here to Help If You Need It
Short lead times for OSHA indicate the potential for a short lead time for employers to get program elements in place. Our team of safety and industrial hygiene professionals are here to help with the things you may not have time to develop. Let’s get the conversation started!


Contributing:
Curtis Leiker, CSP
Certified Safety Professional | ISO 45001 and 14001 Lead Auditor
Curtis Leiker, CSP is a project manager at iSi Environmental. Besides assisting companies with ISO 14001 and 45001 implementation, Curtis manages environmental and safety programs, reporting and compliance issues for aviation, general industry and agricultural facilities. He’s able to see the big picture, but focus on the details and enjoys working to solve EHS issues.